Kaizen
Continual improvement is the mantra for success and being still can be detrimental for progress and staying relevant in the future. Kaizen is a methodology which propagates continuous improvement in an enterprise. Kaizen can be applied anywhere and everywhere.
Key Features of Kaizen
- Expert Quality Management and accredited trainers with real-world experience.
- Instructor-led Quality Management training with multiple training delivery modes.
- Case Studies and Kaizen tools and templated to better understand the concepts.
- Guaranteed to Run Kaizen batches spread across time zones.
- Course completion certificate provided.
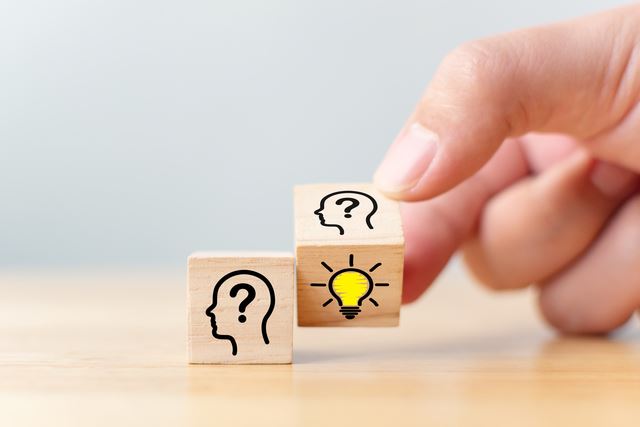
Course Overview
Kaizen Training Program
Kaizen is a philosophy that was introduced in Japan which was all about improvement of systems, people, and programs in continuous manner. Kaizen word means “change for the good” where the workforce across industry sectors can create a culture of ongoing refinement and optimization. This Kaizen training is ideal for individuals and enterprise teams that look to constantly improve their business operations by aligning everyone with Kaizen Principles.
By attending this 1-day Kaizen training program, learners will gain a proper understanding of improving productivity through continual improvement activities across all levels of the organization across industry sectors. With Lean methodology helping organizations to remove waste, Kaizen helps in achieving continuous and incremental improvements which become standard over a period of time.
Target Audience for Kaizen
- Lean Six Sigma Project Team Memebers.
- Lean Facilitators.
- Lean Six Sigma Consultants.
- Process Improvement Managers.
- Change Managers / Change Agents
- Quality Supervisors
- Continuous Improvement Professionals
- Aprofessionals whoa re looking to gain a proper understanding of Kaizen concepts and its implementatio in and organization.
Pre-Requisites
There are no prerequisites/eligibility criteria to take up this Kaizen training.
Exam Format
There is no exam format for this Kaizen training.
Kaizen Agenda
- Introduction
- Understanding the origins of Kaizen
- Making waste visible - identifying the the non-value added activities in your organisation
- Examples of lean Tools to be used to support Kaizen events such as 5s and Value Stream Mapping.
- Three Kaizen approaches - Just Do it, Kaizen Events (PDCA) and Kaizen Blitz
- Root Cause Analysis - Ishikawa (Cause & Effect) and 5 Whys
- How to successfully implement a Kaizen culture?
- How to structure a Kaizen team?
- MBWA - The Gemba Walk
- The Task Board
- Sustaining a Kaizen Culture